Update 3
- fsae-mmi
- Feb 1, 2020
- 3 min read
Over the period of January 13 - January 31, the MMI team has been working on the preparation for the pedal box load testing and the acquisition of parts and materials for the braking system. The team has completed FEA analysis on the main structure of the pedal box and the brake pedal. The main structure has been improved by adding a new master cylinder brace since the test showed weakness in that area. The brake pedal may need to have extra support material added because of the possible yielding in the middle of the pedal as shown by the FEA. The team has asked Dr. Hammami for the availability of the Instron machine which will be used for the validation of the pedal box. Reusable parts like rotors, calipers, and the Brake Over Travel Switch (BOTS), have been removed from the previous car to be used in this years car. The parts list for the other materials has been constructed and will be submitted to start ordering parts. Lastly, the team is completing DXF files to send to machinists in preparation for laser cutting the necessary parts for the pedal box.
The team experienced some challenges when working with getting the parts removed from the previous car. Luckily, the MMI team had the required tools and the guidance of Alan McCallum during the process to help us remove the rotors and calipers. The removal of the Brake Over-Travel Switch (BOTS) was complicated by the arrangement of the hydraulic lines which made it significantly more difficult to get a wrench to the nuts holding it in place. The MMI team eventually figured out which cables to detach in order to get the movement required for us to remove the part. The MMI team also had trouble thinking of different ways to validate our pedal box. There were many different options to apply 2000 Newtons to our project. Options for evaluating the pedal box includes through loading of weights via a strap/chain, loading from a lever to reduce the overall weight needed, and utilizing an Instron machine available on campus. We decided that utilizing an Instron machine would be the safest and most reliable option for load testing the pedal box. The team experienced some challenges when working with getting the parts removed from the previous car. Luckily, the MMI team had the required tools and the guidance of Alan McCallum during the process to help us remove the rotors and calipers. The removal of the Brake Over-Travel Switch (BOTS) was complicated by the arrangement of the hydraulic lines which made it significantly more difficult to get a wrench to the nuts holding it in place. The MMI team eventually figured out which cables to detach in order to get the movement required for us to remove the part. The MMI team also had trouble thinking of different ways to validate our pedal box. There were many different options to apply 2000 Newtons to our project. Options for evaluating the pedal box includes through loading of weights via a strap/chain, loading from a lever to reduce the overall weight needed, and utilizing an Instron machine available on campus. We decided that utilizing an Instron machine would be the safest and most reliable option for load testing the pedal box.
For the period of January 31 - February 14, our main goal will be to submit Approval For Expenditure (AFE) forms to begin the purchasing process for all of our parts and materials. Once the materials are received, the material and associated DXF file will be submitted to the vendor sponsoring UH FSAE for any necessary laser cutting. Our biggest challenge during this time will be ensuring that the necessary funding has been collected to purchase everything the team needs. The FSAE team has been participating in a fundraising campaign that will end February 15. Our goal is to collect enough funds for all of the FSAE teams to complete their builds for the car.
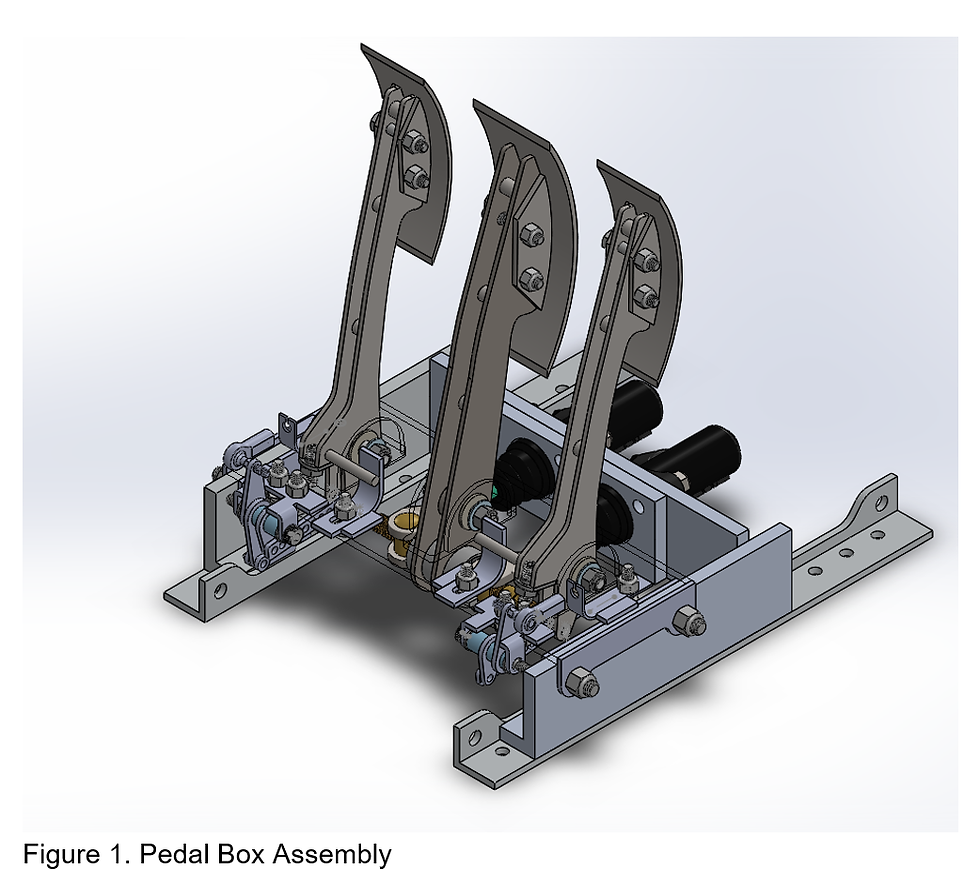
Since the previous update, the pedal box has undergone many modifications. For instance, the master cylinder orientation depicted in Figure 1, our current pedal box, is rear mounted and is therefore facing the driver. Our previous pedal box design featured a forward mounted master cylinder pointing away from the driver. The team chose the rear mounted master cylinder assembly since it would be more compact. The pedals had also been redesigned as well, favoring a more ergonomic shape for the driver and thinner pedals overall.
Aside from the pedal box, the MMI team has also been working on a CAD model for the bell crank. Oil-filled bushings will allow for rotation of the bell-crank about a shoulder-bolt. The arms of the bell-crank will consist of welded tabs on a hollow steel cylinder. This year’s car will feature a cable-driven clutch and a push-pull throttle.
Commentaires