Blog Update #6
- fsae-mmi
- Mar 27, 2020
- 3 min read
Capstone II Blog Post #4

Figure 1: Pedals
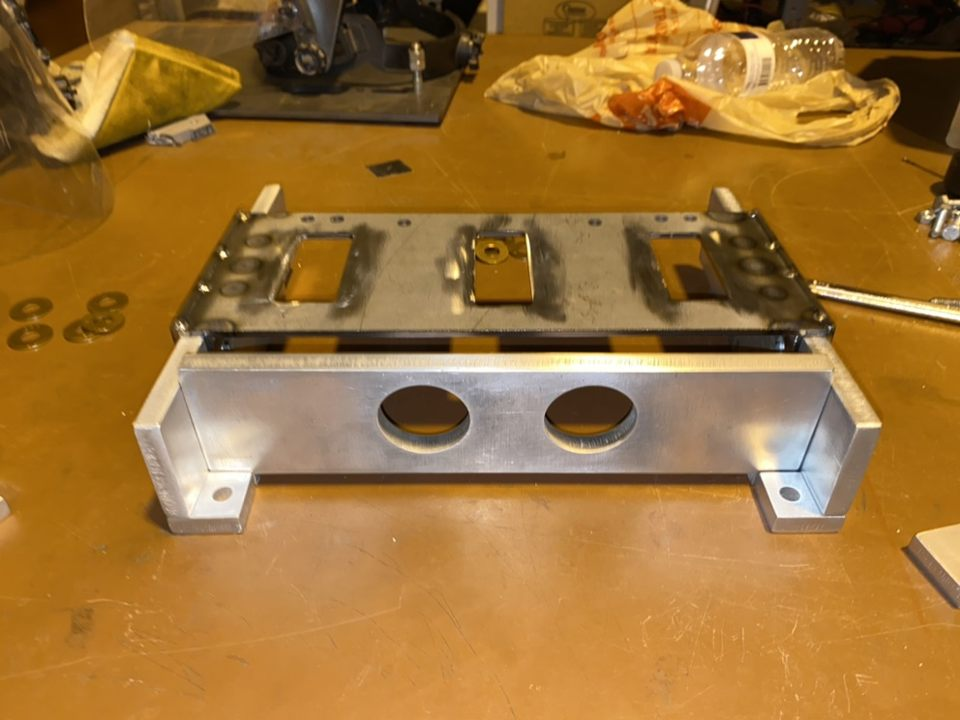
Figure 2: Assembled Configuration of Parts
Over the work period of March 6 - March 20, the MMI team has received the laser cut parts to assemble. Weld surfaces were polished with a flapper wheel for the steel components. Nuts and bolts were then used to jig the pedals into position for welding, as seen in Figure 1. A spare aluminum plate was used to help cool the pedals down after each weld bead. When the front and back supports are welded to the parts, the pedals will be complete. The main body of the pedal box is made of aluminum so the team prepared the parts for welding by smoothening the edges. The edges of the aluminum parts came out rough from the laser-cutting and could contribute to the formation of crack formation during welding. A partial assembly of the main parts is carried out as seen in Figure 2, the partially completed top plate was fitted over the side plates to ensure the dimensions of the parts were correct. The laser-cut parts all came out to be dimensionally consistent with their CAD models, which meant the team was able to proceed with joining the aluminum body. The aluminum parts are with a welder and the team is waiting to hear back.

Figure 3: Clutch/Throttle Pedal Pad Welding Jig
While waiting for the aluminum parts to be welded, fabrication of the pedal pads was commenced. The rolled ⅛” steel plates were cut down to size and aligned with a set of pedal pad tabs jigged to each pedal. Figure 3 shows a partially completed clutch/throttle pedal after having been tack-welded in place. Special care was taken to center the pads with the pedals during the initial tack-welds. Aside from the completion of some of the key components in the pedal box, the FSAE cost report was started as well. Due to COVID-19, the team was not able to do much more.
One of the main challenges that every team faced during this time are the events following COVID-19 pandemic. The team was able to work on the project during spring break, but soon after that, not much work could be done at the shop due to the community social distancing in order to stop the virus from spreading. Around the second week of spring break, a policy of allowing only 4-5 people to work in the shop was implemented. As a result of this policy, some teams have experienced issues working on their parts in the shop.
The team’s plan for the work period March 20 - April 3 is to do as much of the paperwork as we can from home. With the COVID-19 pandemic, many of the counties that feed into the University of Houston system have given a Stay-at-Home order. This means that the shop where the car is being built at ERP has been closed. Because of this, we will not be able to physically work on our project until access is granted by the school system. The team will work on FEA simulations and the cost report in order to complete as much of the paperwork and documentation as possible for the project. Priority will be placed in completing the cost report since it is directly related to the Cost Event for the competition and has the earliest due date of midnight, March 30.
Comments