Update 2
- fsae-mmi
- Nov 16, 2019
- 3 min read
The motivation for our top project idea is to help the UH FSAE team succeed at the 2020 competition in the spring, as in previous years the team has run into various errors and has not been able to fully compete in competition. According to the 2020 FSAE rulebook, the Brake Test is passed when all four wheels lock up and the engine remains running during the braking test. The team has struggled with the Brake Test, in which, failure means disqualification from participating in the Dynamic Events. This means that if we succeed in designing a well-performing brake system, the team will finally be able to fully compete at competition for the first time in the last 3 years.
Between November 1st and 15th, time was spent reducing the overall weight of the pedal box. The base-plate was reduced in size to allow for direct mounting of the master cylinder mount to the mounting rail below. Fastener locations were drafted onto the non-welded components and a full working assembly was made. The figure below details what our final pedal box design looked like prior to the Design Review Presentation

Figure 1: Top-Mounted Master Cylinder Pedal Box Design
Shortly after the Design Review Presentation, the team was notified by the President of FSAE that the chassis length would have to be shortened. The base of the impact attenuator couldn’t be more than 400 mm away from the outside of the tires. The resulting chassis length change conflicts with the top-mounted master cylinder configuration that was originally intended for our pedal box. To accommodate for the change in chassis length, the pedal box is being designed for a floor-mounted configuration.
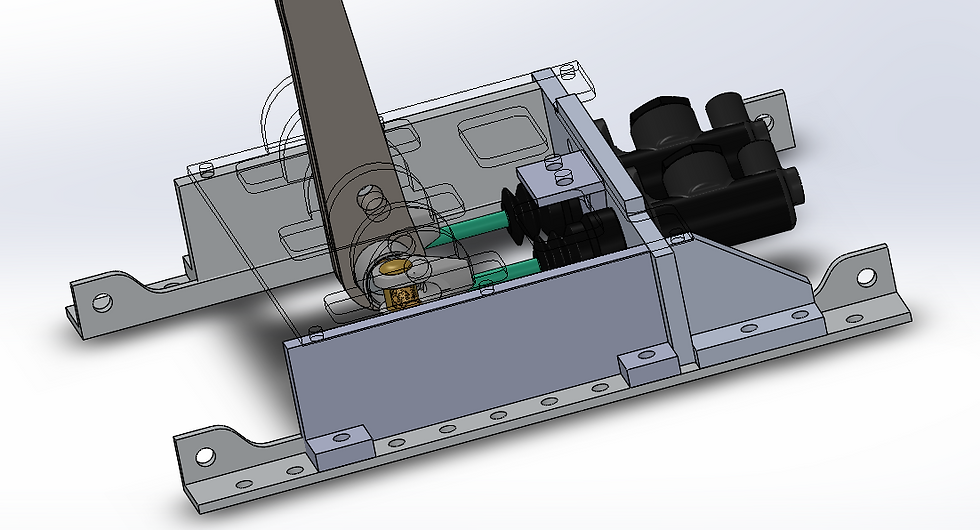
Figure 2: Work-In-Progress Floor-Mounted Pedal Box Design
Some design characteristics between the top-mounted and floor-mounted master cylinder configurations remained consistent, which is shortening the time needed to be spent in designing the new box. Special attention is being paid to ensure the master cylinder mounting plate has enough support to reduce bending during braking operations.
Managing time to keep up with the deadlines set for our project milestones has been challenging when the team has been trying to keep up with their other non-capstone related lectures. Having to redesign the pedal box has set the team back considerably. (Having trouble thinking much more to add) Fortunately, most of the previous FSAE cars at the University of Houston used floor-mounted master cylinders. The team has access to the CAD models from the 2018-2019 car “Sunny”. We have also been able to review the design of the pedal box used on “Gladys”, which is on display in Engineering Building 1. The insight from the designs from the previous competition years has helped reduce the time the team needed to spend generating CAD models of the new pedal box.
So far the MMI team has done a lot of design modifications for the pedal box. The plan for the period of November 15th to 25th will be to make final corrections to the design of the pedal box, make any needed changes to the assembly in OnShape, and then place the pedal box assembly into its correct designated position in the chassis. Once all that is complete, the MMI team will produce CAD drawings for the fabrication of rotors, so that everything can be ready to order by winter. Anticipated challenges and setbacks will include any more modifications to the chassis which would affect the dimensions of the pedal box. For the rotor, the MMI team has determined that the rotors from last year will be reused.
Comentários